Microelectromechanical system (MEMS) accelerometers, important in high-precision fields, have historically encountered issues with temperature drift and stability, which limits their broader application. The recent study addresses these challenges by introducing a MEMS accelerometer that uses advanced self-centering and stiffness control mechanisms. This innovation enhances accuracy and temperature stability, making the device suitable for the most demanding applications. The research opens new doors for the use of MEMS accelerometers in fields where accuracy and consistency are extremely important.
MEMS accelerometers, essential for various high-tech applications, face challenges with temperature-induced resolution deviations. Although they are widely used in electronics, navigation and surveillance systems, their performance is compromised by temperature effects on mechanical and electronic components, leading to inaccuracy. Traditional solutions involve designing heat-insensitive structures and improving manufacturing processes, but their success is limited.
A recent study (doi: 10.1038/s41378-023-00647-4) led by a team of experts from Zhejiang University, published on January 18, 2024, in the journal Microsystems & Nanoengineering, presents an innovative MEMS accelerometer based on stiffness tuning with enhanced accuracy and stability. Featuring self-centering and rigidity control capabilities, this device represents a major advance in accelerometer technology.
The study presents a MEMS accelerometer equipped with a novel dual closed-loop system, integrating DC/AC electrostatic adjustment to effectively adjust the stiffness and calibrate the geometric displacement. This system addresses the common problem of temperature drift, improving device accuracy and reliability. The accelerometer design uses a self-centering closed loop to accurately determine the optimal reference position and a stiffness closed loop to maintain effective stiffness despite temperature changes. Real-time adjustments of the reference position and voltage adjustment allow residual temperature drift to be compensated, achieving a temperature drift coefficient of approximately 7 µg/°C and an Allan bias instability of less than 1 µg.
“Our study represents a major step forward in MEMS technology, offering notable improvements in both accuracy and temperature stability of near-zero rigidity-based accelerometers,” says lead researcher Dr. Zhipeng Ma.
This innovation not only addresses the long-standing challenges of temperature drift, but also paves the way for more reliable and accurate applications in critical fields such as space exploration and environmental monitoring, promising to revolutionize high-precision measurement and control systems.
/General release. This material from the original organization/author(s) may be chronological in nature, and is edited for clarity, style and length. Mirage.News does not take corporate positions or parties, and all opinions, positions and conclusions expressed herein are solely those of the author(s).View in full here.
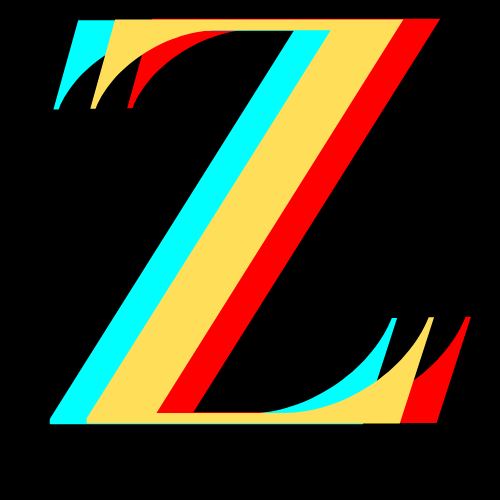