As we all know, technology is a science built on a series of successive events and inventions. Without the wheel there would be no car. Without electricity, there would be no telegraph, no telephone, no radio, no television, no computers, and ultimately, no Internet. Five years ago, futurist Mike Ivicak wrote in his January 1, 2018 article:startupAdvances in technology are “an area in which past events can provide a good indication of how future events will play out.” The forefront of technological progress.”
Fast learning curve
While it may seem steep at times, the learning curve in manufacturing has accelerated with each century since the first industrial revolution. And progress continues to advance. But where are they going?
We have gained momentum, moving from traditional coal- and steam-powered machines to smaller, faster, leaner and cleaner machines, to mechanical assembly, to computer-based assembly, to robotics and machine learning. Where has this brought us?
We are now on the cusp of the most effective and efficient manufacturing processes ever. So, what have we learned from the past that got us here? We've learned that there are fundamental principles that govern both efficiency and effectiveness, such as Six Sigma, lean manufacturing, and other process improvement methodologies. Lean manufacturing principles can significantly reduce waste, optimize resources, and enhance productivity in future manufacturing operations. In his book, Essential tools for process improvementDr. Fred Rispoli explains the importance of prospecting to uncover the true root causes of failure and inefficiency in manufacturing. This derives directly from William Edwards Deming's statistical process control, which gained its place among the new standards of quality control in manufacturing in the twentieth century.
The first industrial robot
Consider that Unimation's first industrial robot in 1961 revolutionized assembly lines, enhancing speed and accuracy. Further advances in robotics and automation will lead to more efficient and flexible manufacturing processes, reducing labor costs and increasing production. The ultimate long-term benefits are countless. Consider the impact robots have already had on surgery, for example.
We have learned the importance of creating technologies that enable and enhance human collaboration, such as enterprise resource planning (ERP) systems. Above all, we have learned that each technology will be outperformed by another over time. Henry Ford's automobile assembly line operated for a century. . . Until Asian car manufacturers came up with a better system by pre-assembling components for each step. Data storage media have evolved from tapes to disks to flash drives. Will crystals be next? Perhaps, since they have a much larger data storage capacity.
What will take us to the next level in manufacturing? Understand that what happened to us here It may not happen to us there It's the first step. As we search for better solutions than ever before, we still need to look back to analyze not only what worked, but also what worked Why He succeeded in getting us here. For example, without lasers, we would never have achieved the absolute precision needed for some important applications, such as engraving and surface marking, as well as the printing of identification numbers. But what prompted the need to apply this technology? Was it simply faster, smarter and cheaper production – or a more pressing, basic need? As we identify the missing elements of the past, we can begin to reshape the future of manufacturing.
Impact of advanced materials
Aviation is perhaps one of the best examples of looking to the past to create a better future. Learning the principles of aerodynamics led to newer and improved designs. Every part of the process has been constantly evolving, from the physical appearance to the materials used to the propulsion systems. Discoveries in metallurgy, polymers and composites have allowed the development of lighter, stronger and more versatile materials for manufacturing. Future manufacturing can leverage advanced materials to create innovative products with improved durability, efficiency, and sustainability.
Even small businesses now have access to the best of today's cutting-edge manufacturing technologies with lower costs. At my company Exothermic Molding, we have been able to provide high-volume 3D printing, receive equipment training, and deliver lower-cost, faster, high-quality prototyping of plastic parts without the need to create molds. We now validate our parts and molds through laser scanning without ever touching them.
The emergence of artificial intelligence
Artificial intelligence (AI) is another important technology for manufacturing. Are we ready to hand over our entire project to AI? At Exothermic, we use AI (as a participant) in daily production meetings to summarize topics and conversations taking place (with voice recognition), and to summarize assigned responsibilities. It works surprisingly well and brings value. We are at the beginning of artificial intelligence and the technological changes it brings. The next step is to explore what it can do for our operation.
According to a study by Deloitte, SMEs across various sectors are increasingly investing in AI technologies to improve operational efficiency and competitiveness. A report from Accenture indicates that small businesses globally are realizing the potential of AI, and are expected to double their adoption rates over the next few years. This reflects a broader trend of AI becoming more accessible to small businesses.
Artificial Intelligence is changing the game for SMEs
For example, companies like Smith Robotics, a robotics manufacturer, have harnessed artificial intelligence to enhance the accuracy and flexibility of their robotic systems. The ability of this small-scale process to leverage AI demonstrates the democratization of advanced technologies, enabling even niche manufacturers to compete on the cutting edge.
In a similar vein, precision machining company Quantum CNC has used AI algorithms to optimize toolpaths, reduce production time and reduce material waste. This exemplifies how AI is not limited to large-scale enterprises but is becoming a game-changer for smaller players seeking efficiency gains.
In addition, Innovate Tech Solutions, a small electronics assembler, has adopted AI-based quality control systems. Through the use of computer vision and machine learning algorithms, defects are significantly reduced and product reliability is enhanced. These success stories demonstrate that AI integration is not specific to a particular sector, but is versatile and adaptable to diverse manufacturing environments.
In today's environment, we view manufacturing as a more holistic endeavour. It's not just about making a product. It's about understanding the needs of the market, learning how to best meet those needs, and anticipating future needs — as in the Amazon example above — all while considering and respecting the needs of every stakeholder, from customer to supplier to employee, and ultimately the planet. Understanding how we have failed to do this in the past will help us adjust our mindset as we create our future.
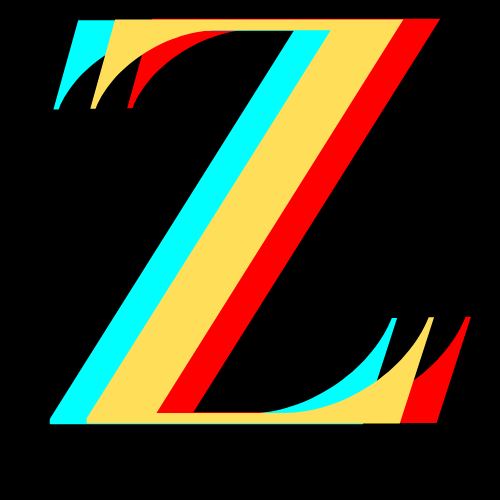